The growth of the F-35 program at Northrop Grumman has been attributed to the pursuit of inventive and resourceful approaches to sustain rigorous production rates, while concurrently upholding elevated benchmarks for accuracy, excellence, and cost-effectiveness.
The manufacturing expertise of the company plays a pivotal role in its achievement of providing support to the most advanced fighter aircraft.
Towards the end of 2001, Northrop Grumman was designated as a primary member of an industry team led by Lockheed Martin, aimed at manufacturing the center fuselage of the F-35 Lightning II, a versatile and stealthy aircraft, in a substantially increased quantity. Achieving program success would necessitate the integration of advanced robotics technology with enhanced automation capabilities.
Northrop Grumman is known for its production of various mission system capabilities, one of which is the integrated Communications, Navigation and Identification (iCNI) system. This system serves as a central nervous system for advanced fighter aircraft. Furthermore, the team offers modification management, integration of product support, and repair of components for the F-35.
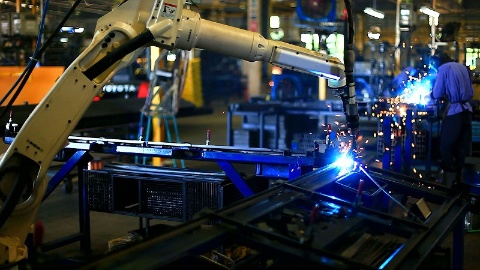
The implementation of automation is expected to enhance the production of the F-35 aircraft.
Glenn Masukawa, the F-35 lead at Northrop Grumman, stated that the utilization of automation and robotics was crucial in achieving the F-35 program’s objective of maintaining a consistent high-volume production. The requirement for affordability necessitated significant cost reductions over a period of time.
Northrop Grumman has previously spearheaded the development of automated manufacturing systems aimed at producing essential subassemblies for military aircraft. Nevertheless, the revised standard called for a manufacturing cycle of 24 hours, a challenging objective that would put to the test even the most sophisticated airplane production facilities across the globe.
Drawing Lessons from Automotive Industry to Establish an Integrated Manufacturing System
In order to address this challenge, the organization sought guidance from a similar high-volume manufacturing sector within the nation, namely the United States’ automotive industry.
According to Scott Johnson, the integrated product team lead for the F-35 center fuselage, a collaboration was established with KUKA Systems North America, an automation technology firm located in Detroit that specializes in the integration of assembly lines for the automotive sector. We integrated their comprehension of automation and automotive assembly lines with our proficiency in aerospace tooling. The Integrated Assembly Line (IAL) is a culmination of the most effective production methodologies from both industries.
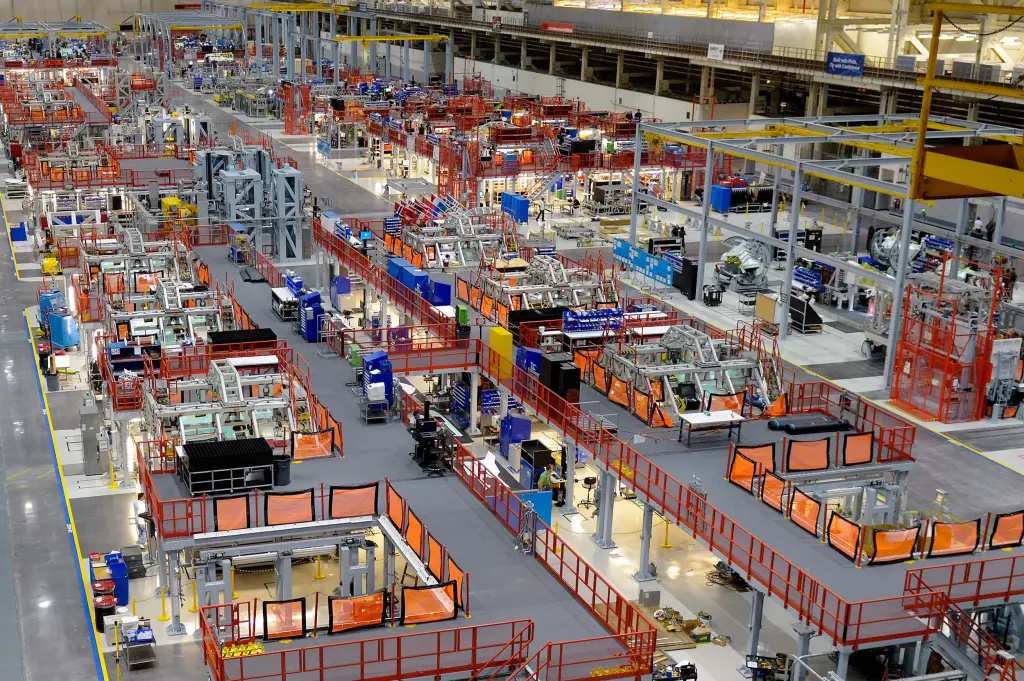
According to the speaker, the IAL presented a chance to eradicate isolated components in the corporation’s F-35 production procedure and establish a fully unified manufacturing system.
Achieving Production Targets
The IAL with a U-shaped configuration is situated at the Aircraft Integration Center of Excellence owned by Northrop Grumman in Palmdale, California. The system is composed of over one hundred construction stations and twenty-two automated mechanisms that have been specifically developed to improve the overall quality, safety, and cost-effectiveness of the process. At present, the IAL is functioning at maximum capacity and is able to finalize an F-35 center fuselage within a time frame of 30 hours, thereby resulting in a production cycle of 1.25 days.
As of now, Northrop Grumman has successfully supplied 850 center fuselages for the F-35 aircraft. The organization intends to distribute 149 of these units solely in the year 2021.
Engaging in a situation where three individuals are confronting a single individual.
As per Johnson’s assertion, a noteworthy feature of the IAL is its ability to manufacture the Conventional Takeoff and Landing (CTOL), Carrier Variant (CV), and the Short Takeoff Vertical Landing (STOVL) variants of the F-35 concurrently.
According to Johnson, all three variations employ identical foundational tooling. The distinctive factor of our organization lies in the highly resilient worldwide supply chain of Northrop Grumman.

The author observes that the supply chain team collaborated in devising a systematic approach for transporting components to the IAL through the utilization of specialized containers known as “shadow boxes.” The foam cutouts enclosed within each box are tailored to accommodate the precise components that mechanics are required to mount onto the center fuselage. After the installation of said components, the team proceeds to retrieve the vacated container and replenish it in preparation for the subsequent variation in the production sequence. This facilitates the process of producing multiple variants seamlessly, utilizing a solitary production line.
According to Masukawa, this uncomplicated yet highly efficient procedure results in almost flawless precision when it comes to fitting the appropriate component onto the correct aircraft.
The integration of next-generation technology has facilitated both affordability and innovation in various industries.
Undoubtedly, the lifespan of production equipment is finite, and the pace of technological advancements is incessant.
According to Masukawa, there is a continuous search for prospects to implement novel manufacturing technologies in order to enhance the efficiency and affordability of the F-35 build procedures. The objective is consistently to optimize our utilization of automation.
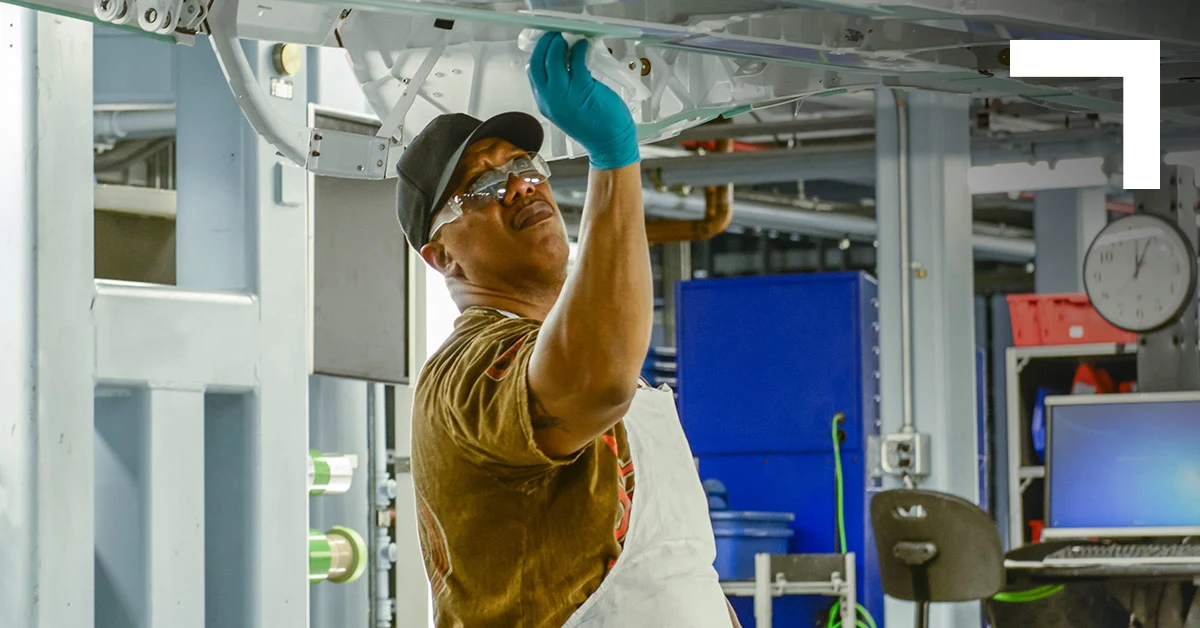
As Masukawa observes, the establishment of a thriving advanced aircraft production ecosystem necessitates the involvement of a diverse team that is both talented and committed.
According to the speaker, the organization depends on the skills and commitment of various individuals, such as mechanics, manufacturing engineering teams, line managers, quality inspectors, and a worldwide supply chain comprising over 250 local and foreign suppliers. The utilization of technology in the most efficient and economical manner to meet the demands of both present and future customers is primarily driven by ingenious individuals, rather than solely relying on automation and robotics.
Download The Radiant App To Start Watching!
Web: Watch Now
LGTV™: Download
ROKU™: Download
XBox™: Download
Samsung TV™: Download
Amazon Fire TV™: Download
Android TV™: Download